Deep groove ball bearings are a ubiquitous component in many mechanical applications, yet the intricacies of their design and functionality are often underappreciated. Known for their ability to support radial and axial loads simultaneously, these bearings are pivotal in a myriad of industries from automotive to aerospace, showcasing their versatility and reliability.
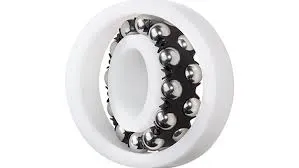
At the heart of their functionality lies the design principle the deep grooves on both the inner and outer rings form a channel along which the balls run. This unique design allows for higher load capacity compared to other types of ball bearings, such as angular contacts. The deep groove accommodates both radial and axial loads, making them indispensable for applications with varied operational demands.
The success story of deep groove ball bearings begins with their unparalleled efficiency. Thanks to their precision engineering, these bearings minimize frictional losses, translating to higher rotational speeds and reduced energy consumption. This is particularly significant in the automotive industry, where efficiency equates to fuel savings and reduced emissions, aligning with contemporary environmental standards.
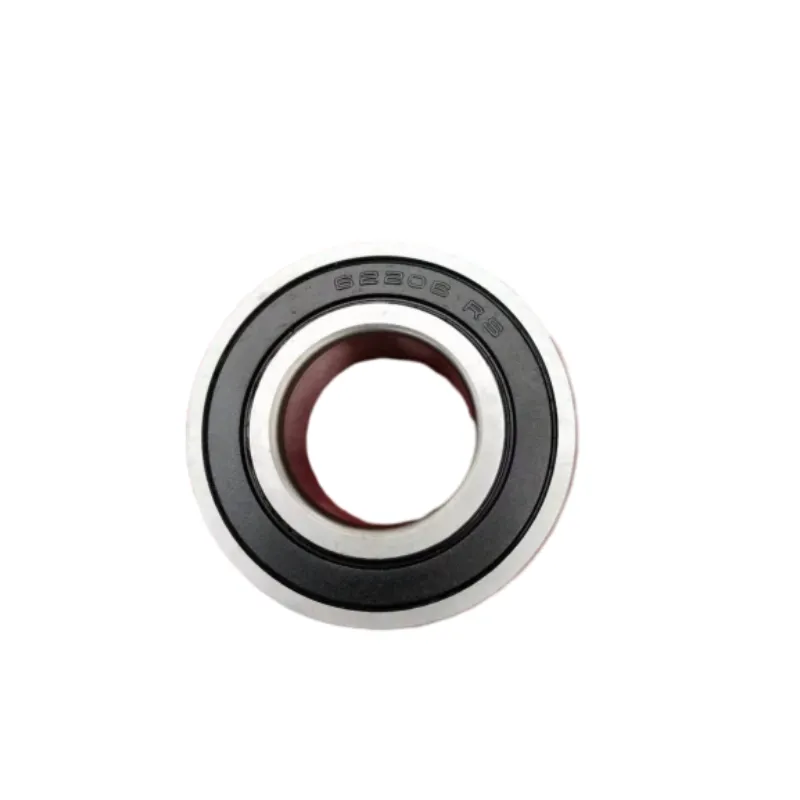
The reliability of deep groove ball bearings, underpinned by their design, contributes to prolonged service life and minimal maintenance. In industrial settings, where downtime equates to substantial financial losses, the dependability of these bearings is paramount. The precise alignment of the ball with the race ensures uniform load distribution, which prevents wear and extends operational lifespan, making them a preferred choice for businesses prioritizing longevity and cost-effectiveness.
For engineers and product designers, the choice of material in deep groove ball bearings adds another layer of specialization. High-quality materials such as stainless steel or ceramic are often selected based on the application environment, offering resistance to corrosion and compatibility with extreme temperatures. This adaptability is crucial for specialized applications, such as in chemical processing plants or food production facilities, where material integrity cannot be compromised.
deep groove ball bearing meaning
Moreover, contemporary advances in bearing technology have seen the development of hybrid versions, which integrate ceramic balls with metal races. These hybrids hold significant advantages in terms of reduced weight, lower friction, and enhanced speed capabilities, opening up new possibilities in industries demanding cutting-edge performance.
Experts relying on deep groove ball bearings appreciate not only their robustness but also the ease of installation and interchangeability across different systems. Standardization in dimensions and the availability of various sizes ensure that these components fit seamlessly into diverse applications without the need for extensive modifications.
Deep groove ball bearings embody a blend of time-tested engineering principles and modern innovation. Their continual evolution aims to meet the rising demands for efficiency and reliability in an increasingly performance-driven world. By mastering the inherent qualities and realizing the full potential of these bearings, industries can drive forward their technical applications with confidence and precision.
In conclusion, deep groove ball bearings stand as a testament to mechanical engineering’s ability to create components that are both simple and complex in function. Their role in enhancing machine operations, optimizing performance, and offering sustainable solutions aligns perfectly with the growing global emphasis on sustainable and efficient industrial practices.