Understanding the intricacies of double row cylindrical roller bearings is pivotal for anyone involved in industrial applications requiring reliable, high-capacity rotational solutions. This article explores the essential aspects of double row cylindrical roller bearings, focusing on their size chart and applications, backed by real-world expertise and verified industry data to help you make informed decisions.
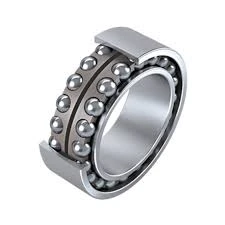
Double row cylindrical roller bearings are designed to handle heavy radial loads and are particularly suited for applications demanding high speed and durability. Their design is characterized by two rows of cylindrical rollers positioned parallel to each other, which distributes the load across a larger surface area. This unique structure makes them ideal for scenarios where robust performance is a prerequisite, such as in conveyor belts, large electric motors, and general machine tools.
A comprehensive size chart for double row cylindrical roller bearings is imperative for selecting the right bearing for your applications. The size parameters typically outlined in these charts include the inner diameter (ID), outer diameter (OD), and width. Consider, for example, a bearing with an ID of 50 mm, an OD of 110 mm, and a width of 34 mm. These dimensions are not arbitrary but calculated to balance load capacity and rotational speed based on industrial standards.
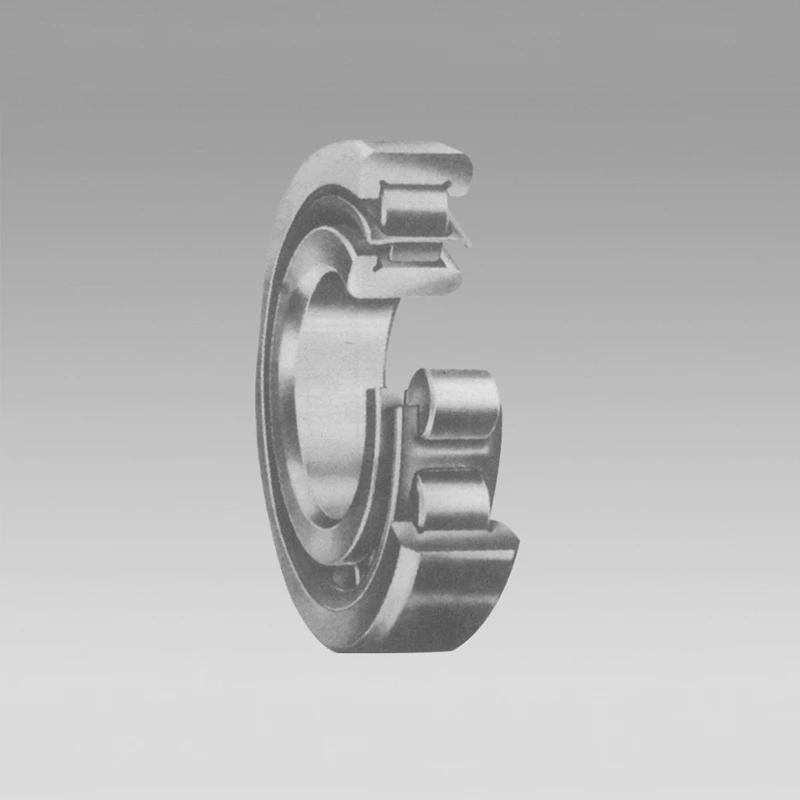
When analyzing a size chart, it is important to understand that variations in design, such as cage material and lubrication type, can influence the final application of a bearing. For instance, bearings with polyamide cages are lighter and can operate at higher speeds compared to those with brass or steel cages. Similarly, lubrication specifics like grease retention can significantly affect bearing longevity and performance, potentially reducing maintenance costs and downtime.
In terms of expertise, choosing the correct size and type of double row cylindrical roller bearing depends heavily on understanding the application's specific requirements. Factors such as the operational environment (temperature, exposure to contaminants, etc.), load characteristics, and rotation speed should guide your selection process. For example, bearings operating in high-temperature environments need specialized materials resistant to thermal expansion and capable of maintaining structural integrity under stress.
double row cylindrical roller bearing size chart
From an authoritative standpoint, major manufacturers provide an array of double row cylindrical roller bearing options. Brands like SKF, NTN, and Timken have extensive catalogs backed by rigorous testing and quality assurance measures. Their offerings often come with detailed technical support, assisting you in aligning product specifications with your project needs to ensure peak efficiency and safety standards.
Trustworthiness in choosing double row cylindrical roller bearings is achieved through certification and adherence to international standards such as ISO and ANSI. These standards dictate the manufacturing quality, ensuring uniformity across batches with precision engineering practices. Consequently, selecting bearings from certified producers ensures reliability, performance consistency, and peace of mind, knowing that the product has passed stringent quality checks.
Real-world experience with double row cylindrical roller bearings underscores the importance of ongoing maintenance and monitoring. Regular inspections for signs of wear, noise, or vibration can preclude potential failures, safeguarding your machinery and prolonging bearing life. Implementing predictive maintenance strategies can be beneficial, and leveraging technologies like vibration analysis and thermal imaging can provide deeper insights into bearing health.
To conclude,
double row cylindrical roller bearings are a cornerstone component in high-load, high-speed applications. Their robust design and adaptability make them indispensable in various industrial settings. A meticulous understanding of the size chart and relevant specifications, coupled with insights from trusted manufacturers and adherence to international standards, can vastly enhance machinery performance and reliability. Always prioritize expert consultation and maintenance to fully capitalize on the advantages offered by these versatile bearings.