Deep groove ball bearings play a vital role in numerous engineering applications, known for their efficiency in handling combined radial and axial loads at high speeds. Their versatile design makes them an invaluable component across various industries, including automotive, aerospace, and manufacturing. Having the right understanding and calculations regarding these bearings can significantly impact machinery performance and longevity.
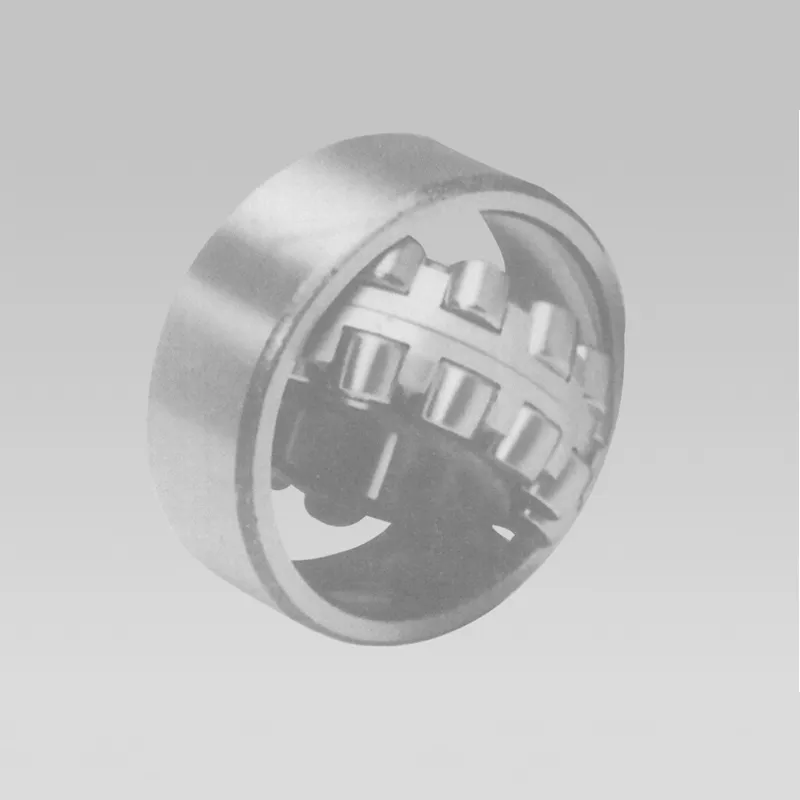
Professionals in the field recognize the significance of precise calculations when dealing with deep groove ball bearings. These calculations ensure optimal bearing performance, enhance the lifespan of machinery, and prevent costly downtime or failures. The calculation process involves several critical parameters, which include load ratings, speed capabilities, and lubrication requirements.
Load rating calculation is essential for determining the appropriate bearing size and type for specific applications. The dynamic load rating (C) indicates the bearing's capability to sustain a specific load for a million revolutions. Meanwhile, the static load rating (C0) assesses the bearing's ability to withstand stationary loads without excessive deformation. Both of these metrics are crucial for engineers when selecting the correct bearing for an application, ensuring reliability under various operational conditions.
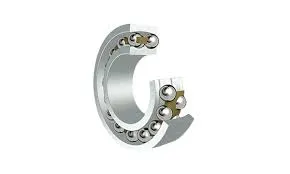
Speed capability is another crucial factor in bearing calculation. The maximum operational speed of a deep groove ball bearing is determined by factors including bearing size, design, and the type of lubricant used. Bearings must be chosen to match the required speed of the operation without compromising performance or safety. Speed ratings often dictate the operational limits, preventing overheating and subsequent failure, thereby maintaining the integrity of machinery.
Lubrication calculation is an integral aspect that often gets overlooked. Proper lubrication minimizes friction between the contacting surfaces inside the bearing, thus significantly reducing wear and tear. It’s not just about the type of lubricant, but also about its viscosity and the appropriate lubrication system for the specific application, which can range from grease-packed bearings to complex oil delivery systems.
deep groove ball bearing calculation
Thermal equilibrium calculations are equally essential when dealing with high-speed or high-load conditions. These calculations help assess whether the bearing can dissipate the heat generated efficiently. Excessive heat can lead to lubricant breakdown, premature aging of bearing materials, and eventual bearing failure. Understanding the thermal pathways and selecting the correct lubrication and cooling methods can enhance performance and extend the bearing’s service life.
Moreover, environmental factors such as moisture, dust, or even extreme temperatures should be considered in bearing selection and calculation. For example, in highly corrosive environments, stainless steel or coated bearings might be preferred to enhance resistance against corrosion, thereby enhancing reliability and decreasing maintenance frequency.
Experts always highlight the need for proper installation and alignment of deep groove ball bearings. Misalignment can lead to uneven load distribution, resulting in increased stress and reduced efficiency. Accurate alignment minimizes unnecessary strain and enhances bearing performance and longevity.
Finally, having a routine condition monitoring program can make a significant difference. Regular check-ups help in early identification of potential issues such as lubrication breakdown or unusual vibrations, thus preventing unexpected failures.
In conclusion, precise and comprehensive calculation of deep groove ball bearings is paramount in the field of mechanical engineering. It demands a rigorous understanding of various parameters such as load ratings, speed capabilities, lubrication, and environmental conditions. Mastery in these calculations not only enhances machinery performance but also ensures safety, reliability, and efficiency, embodying the principles of Experience, Expertise, Authoritativeness, and Trustworthiness in the engineering domain.