Understanding Cylindrical Roller Bearings A Comprehensive Overview
Cylindrical roller bearings, an essential component in various mechanical systems, play a crucial role in facilitating smooth and efficient motion while withstanding substantial loads. These bearings, as the name suggests, feature cylindrical rollers that are uniformly distributed around the bearing's inner and outer rings, providing a high radial load capacity and excellent performance in applications where heavy loads are prevalent.
The primary design of a cylindrical roller bearing consists of an inner ring, an outer ring, cylindrical roller elements, and a cage. The cylindrical shape of the rollers allows for a larger contact area between the roller and raceway, distributing the load evenly and reducing stress points. This design characteristic makes them particularly suitable for applications requiring high radial loads, such as crane hooks, rolling mills, and industrial machinery.
One of the key advantages of cylindrical roller bearings is their ability to handle high radial loads without significant deformation. The absence of an offset between the roller axis and the bearing axis ensures minimal friction, thus reducing heat generation and increasing service life. Additionally, the cage, usually made from steel or brass, keeps the rollers separated and aligned, preventing direct contact and potential damage.
However, it's important to note that cylindrical roller bearings have limited thrust load capacity due to their design. They are primarily designed for radial loads and may not perform optimally under significant axial loads They are primarily designed for radial loads and may not perform optimally under significant axial loads
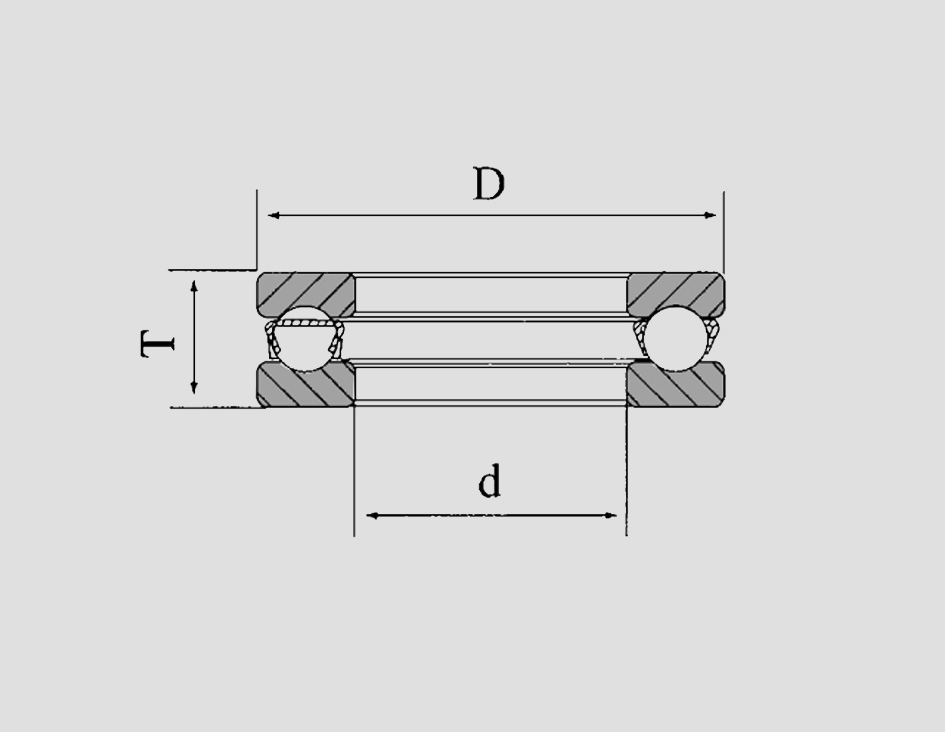
They are primarily designed for radial loads and may not perform optimally under significant axial loads They are primarily designed for radial loads and may not perform optimally under significant axial loads
what is cylindrical roller bearing. For applications requiring both radial and axial support, thrust cylindrical roller bearings or combined bearings can be employed.
Installation and maintenance of cylindrical roller bearings are critical factors influencing their performance and longevity. Proper lubrication is essential to minimize wear and tear, reduce friction, and prevent premature failure. Regular inspection for signs of fatigue, damage, or excessive wear should also be conducted.
In conclusion, cylindrical roller bearings are versatile and robust components that excel in handling high radial loads in demanding industrial settings. Their design, characterized by cylindrical roller elements, ensures efficient load distribution, low friction, and extended service life. However, they necessitate careful consideration during selection, installation, and maintenance to ensure optimal performance and reliability. As technology continues to advance, cylindrical roller bearings remain a staple in industries ranging from automotive to aerospace, testament to their proven effectiveness and efficiency.