Cylindrical roller bearings are pivotal components in various industrial applications due to their exceptional radial load-bearing capacity and minimal friction. Understanding the different types available is essential for optimizing machinery performance and ensuring longevity.
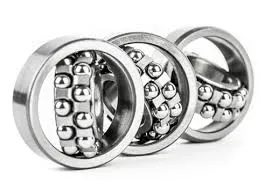
Cylindrical roller bearings come in several variations, each designed for specific needs and environments in which they operate. The most common types include single-row, double-row,
and multi-row cylindrical roller bearings. Each type is characterized by its unique structural design, making it suitable for different levels of load and speed requirements.
Single-row cylindrical roller bearings are the most fundamental type and are widely used in applications where space is a constraint, but high load capacity is necessary. These bearings are designed to handle large radial loads but have limited thrust capabilities. The open design allows for greater lubrication flow and cooling, making them suitable for applications where high speeds are critical, such as in electric motors and generators.
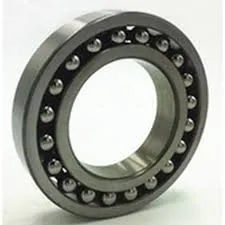
Double-row cylindrical roller bearings offer increased radial capacity compared to their single-row counterparts. The additional row of rollers provides stability and can support higher loads, while still maintaining the ability to handle shock and vibration effectively. They are often employed in heavy machinery, gearboxes, and rolling mills, where robustness is a necessity.
For applications demanding extreme load handling, multi-row cylindrical roller bearings are the ideal choice. These bearings are manufactured with three or more rows of rollers aligned in parallel. The multi-row design not only increases load capacity but also improves rigidity, making them indispensable in industries such as mining, construction, and steel production. Their ability to sustain significant radial loads with minimal space requirements makes them an engineering marvel.
types of cylindrical roller bearing
Cylindrical roller bearings can also be classified according to their cage design. The cage is a crucial component that keeps the rollers evenly spaced as they rotate. Common cage designs include pressed steel, machined brass, and polyamide. Pressed steel cages are favored for their lightweight and cost-effectiveness, suitable for high-speed applications. Machined brass cages are more robust and durable, typically used where reliability under demanding conditions is paramount. Polyamide cages, on the other hand, offer quieter operation and reduced friction, making them ideal for applications where noise reduction is crucial.
An important subset of cylindrical roller bearings is the full-complement type, which maximizes load capacity by eliminating the cage. These bearings contain the maximum number of rollers and are used in applications requiring high load with low-to-moderate speed operations. They are commonly found in crane sheaves, gearbox rear supports, and plastic extruders, where space is less of a concern.
Selecting the right type of cylindrical roller bearing is critical for equipment efficiency and longevity. Factors such as load requirements, speed, temperature, and environmental conditions must all be considered when choosing a bearing. Failure to select the appropriate type can lead to premature failure, increased maintenance costs, and inefficient operation.
Moreover, advancements in material science and manufacturing techniques have led to the development of bearings with enhanced features, such as those with special coatings or heat treatments that resist wear and corrosion, extending their operational life even further. Collaborating with manufacturers or suppliers with extensive expertise can provide insights into these innovations, helping to tailor solutions that match specific industrial needs.
In conclusion, cylindrical roller bearings are integral components that support machinery across various industries. Their diverse types, each with unique attributes, ensure that they meet the demanding requirements of modern engineering applications. Whether it's speed, load capacity, or durability, selecting the right cylindrical roller bearing type can markedly enhance operational efficacy and equipment dependability. Therefore, understanding the specific needs of your application and the characteristics of each bearing type is crucial in optimizing performance and achieving long-term success.