Taper roller bearings are an essential component of many industrial applications, providing a means of transferring load and reducing friction in rotating machinery. The material selection for these bearings is crucial, as it directly affects the performance, durability, and reliability of the system they support.
When choosing materials for taper roller bearings, engineers must consider several factors, including the operating environment, load conditions, speed requirements, and temperature extremes. Common materials for taper roller bearings include high-carbon chromium steel, stainless steel, ceramics, and various alloys. Each material offers its own set of benefits and drawbacks.
High-carbon chromium steel is the most widely used material for taper roller bearings due to its excellent balance of hardness, toughness, and wear resistance. This material can be through-hardened for increased durability or case-hardened for better fatigue life. However, it may not perform well in corrosive environments or at very high temperatures.
Stainless steel bearings are ideal for applications where corrosion resistance is paramount. They offer good strength and oxidation resistance but may not have the same load capacity or fatigue life as high-carbon chromium steel. Stainless steel is also more expensive than other options.
Ceramic materials, such as silicon nitride, are gaining popularity for use in taper roller bearings because of their low density, high hardness, and excellent resistance to heat and corrosion
Ceramic materials, such as silicon nitride, are gaining popularity for use in taper roller bearings because of their low density, high hardness, and excellent resistance to heat and corrosion
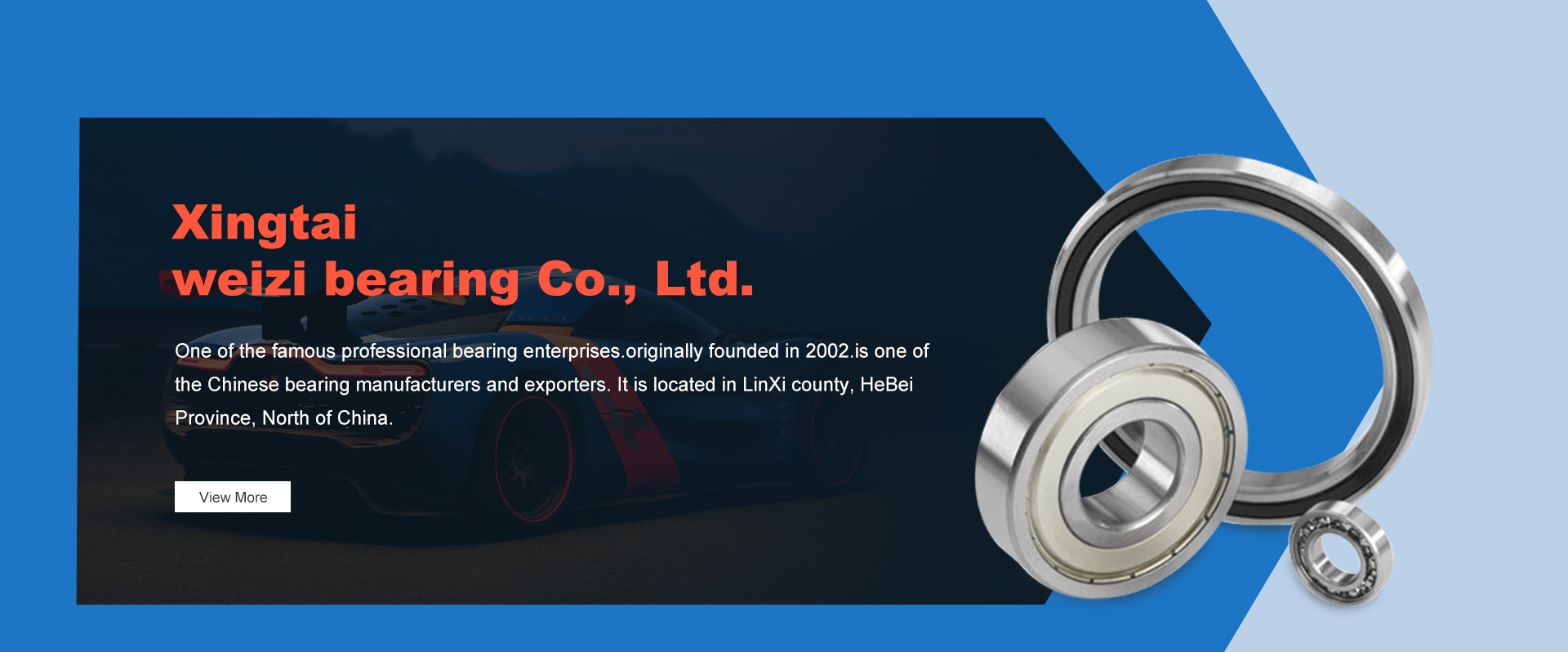
Ceramic materials, such as silicon nitride, are gaining popularity for use in taper roller bearings because of their low density, high hardness, and excellent resistance to heat and corrosion
Ceramic materials, such as silicon nitride, are gaining popularity for use in taper roller bearings because of their low density, high hardness, and excellent resistance to heat and corrosion
taper roller bearing material. Ceramic bearings can operate at higher speeds with less lubrication than their metal counterparts. However, they are brittle and sensitive to impact loads, which can limit their use in certain applications.
Special alloys like tool steels or maraging steels may be chosen for high-performance taper roller bearings that require exceptional strength and wear resistance. These alloys often undergo specialized heat treatments to optimize their properties for specific tasks.
In addition to the base material selection, the design of taper roller bearings also plays a significant role in their effectiveness. Features such as the rolling element geometry, cage design, and lubrication methods all contribute to the overall performance of the bearing. Advanced coatings like titanium nitride or diamond-like carbon can further enhance the surface properties of taper roller bearings, providing additional protection against wear and corrosion.
Ultimately, the choice of material for taper roller bearings depends on a careful analysis of the application requirements and cost considerations. By selecting the right material and designing efficient bearing systems, engineers can ensure that their machinery operates reliably and efficiently under even the most demanding conditions.