The Intricacies of Deep Groove Ball Bearings in SolidWorks
In the world of mechanical engineering and computer-aided design, the representation and simulation of deep groove ball bearings (DGBBs) in software like SolidWorks is a topic that bridges the gap between theoretical knowledge and practical application. A deep groove ball bearing is a type of rolling-element bearing that uses balls to maintain the separation between the bearing races. It is designed to accommodate both radial and axial loads, making it versatile across various machinery applications.
When modeling DGBBs in SolidWorks, engineers can create highly precise digital replicas, which are essential for predicting performance, conducting stress analyses, and optimizing part dimensions. By harnessing the powerful tools within SolidWorks, designers can visualize how the bearing will interact with other components, ensuring proper fit and function.
One of the primary challenges in modeling a DGBB in SolidWorks is capturing the intricate internal geometry of the bearing. This includes accurately representing the curvature of the raceways, the size and number of balls, and the clearances between them. The precision required for these elements is crucial, as even small deviations can significantly impact the bearing's load capacity, lifespan, and rotational accuracy.
To achieve such precision, SolidWorks offers advanced modeling techniques, including the use of sketch relations, dimension drives, and assembly constraints
To achieve such precision, SolidWorks offers advanced modeling techniques, including the use of sketch relations, dimension drives, and assembly constraints
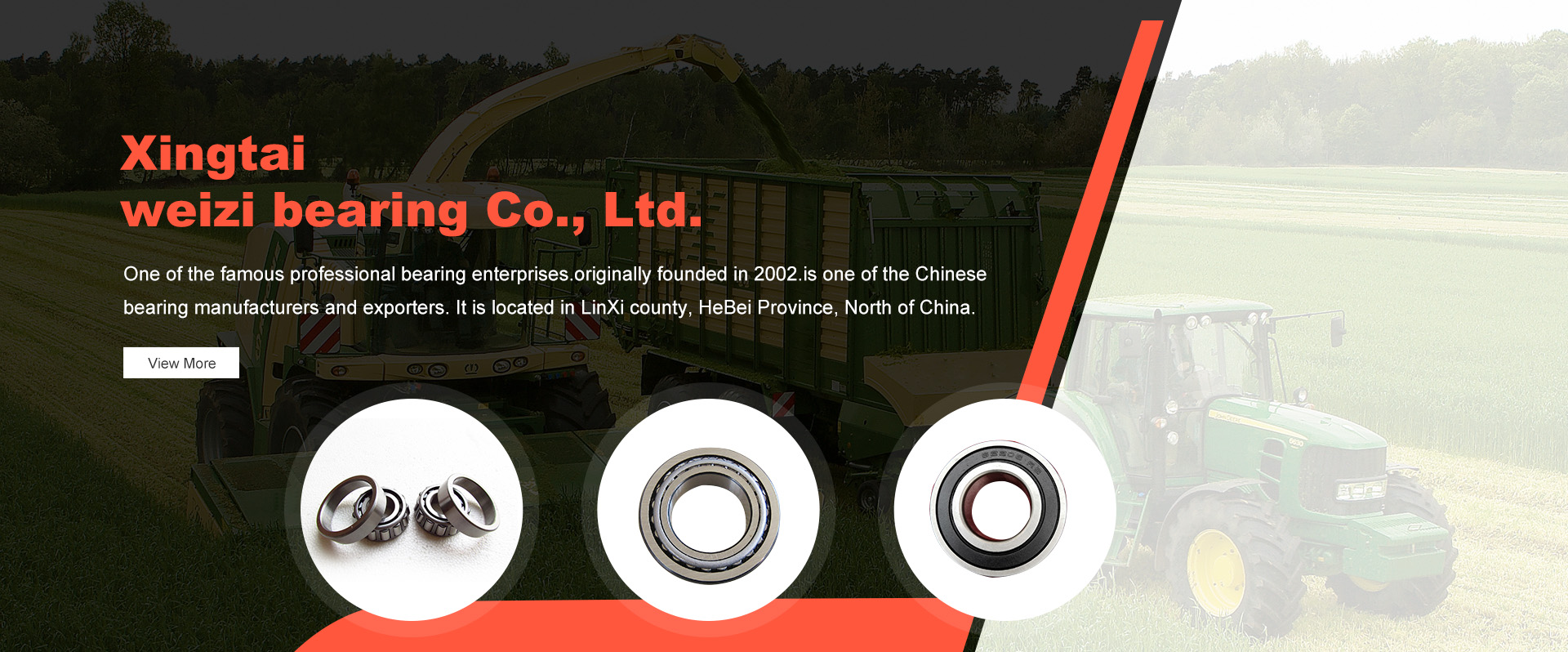
To achieve such precision, SolidWorks offers advanced modeling techniques, including the use of sketch relations, dimension drives, and assembly constraints
To achieve such precision, SolidWorks offers advanced modeling techniques, including the use of sketch relations, dimension drives, and assembly constraints
deep groove ball bearing solidworks. These tools allow engineers to define the geometric relationships between the bearing's components accurately, ensuring that the digital model behaves realistically under various operational conditions.
Moreover, SolidWorks provides robust simulation capabilities that enable engineers to test their designs under different loads and speeds. For DGBBs, this means evaluating factors such as contact stresses between the balls and races, fatigue life, and heat generation. Such simulations are invaluable for iterating designs before physical prototypes are manufactured, saving time and reducing costs associated with trial-and-error approaches.
In conclusion, the integration of deep groove ball bearings into SolidWorks models represents a pinnacle of modern design and analysis. By faithfully reproducing the complexities of these bearings, engineers can optimize their designs, anticipate potential issues, and ultimately create more efficient and reliable mechanical systems. As technology continues to advance, the synergy between hardware components like DGBBs and software platforms like SolidWorks will only become more critical in driving innovation and improving product development processes.