Choosing Between Cylindrical Roller Bearings and Ball Bearings
In the world of mechanical engineering, selecting the right type of bearing is crucial for ensuring optimal performance, efficiency, and longevity of machinery. Two common types of bearings are cylindrical roller bearings and ball bearings, each with its own unique set of advantages and disadvantages. This article aims to provide a comparative analysis between these two bearing types to help engineers make informed decisions based on their specific application requirements.
Cylindrical roller bearings, as the name suggests, use cylindrical rollers to support loads. These bearings are designed to handle heavy radial loads and are particularly effective in applications where space is limited. The cylindrical shape of the rollers allows for increased contact area with the inner and outer rings, distributing the load more evenly and reducing stress concentrations. This makes them ideal for heavy-duty equipment such as conveyor belts, large electric motors, and gearboxes.
On the other hand, ball bearings utilize spherical balls to maintain separation between moving parts. They are known for their ability to handle both radial and axial loads, making them versatile in various applications. Ball bearings typically have lower friction and can operate at higher speeds compared to cylindrical roller bearings. Their compact size also makes them suitable for smaller, more compact machinery such as dental drills, computer hard drives, and automotive wheel hubs.
When comparing durability, cylindrical roller bearings generally have a higher capacity for load carrying due to the larger contact patch between the roller and races
When comparing durability, cylindrical roller bearings generally have a higher capacity for load carrying due to the larger contact patch between the roller and races
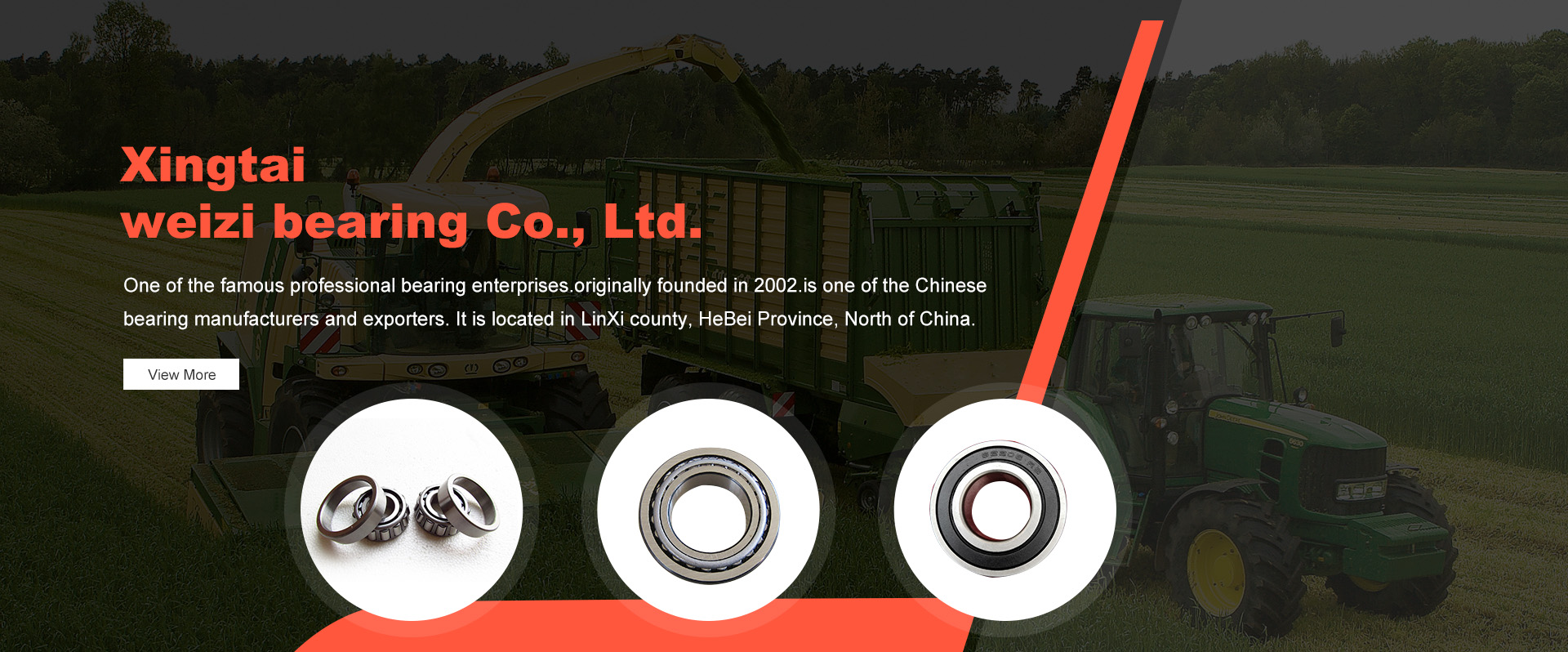
When comparing durability, cylindrical roller bearings generally have a higher capacity for load carrying due to the larger contact patch between the roller and races
When comparing durability, cylindrical roller bearings generally have a higher capacity for load carrying due to the larger contact patch between the roller and races
cylindrical roller bearing vs ball bearing. However, they may not perform well under impact loads or high-speed applications because of their design. Ball bearings, while capable of handling combined loads, may not withstand extremely heavy radial loads as effectively as their cylindrical counterparts.
In terms of maintenance, both types of bearings require lubrication to minimize wear and tear. However, cylindrical roller bearings might require more frequent lubrication due to the increased surface area in contact during operation. Additionally, if one roller fails in a cylindrical roller bearing, it could potentially lead to progressive failure since all rollers share the load equally; whereas in a ball bearing, each ball operates independently, allowing for some redundancy if one were to fail.
The choice between cylindrical roller bearings and ball bearings depends largely on the specific needs of the application. For heavy radial loads and limited space, cylindrical roller bearings are often preferred. For situations requiring both radial and axial load support, as well as high-speed capabilities, ball bearings might be the better option. Engineers must consider factors such as load type, speed requirements, space constraints, and maintenance schedules when selecting the most appropriate bearing for their machinery. By understanding the strengths and weaknesses of each type, engineers can ensure that their machines operate efficiently and reliably for extended periods.