Cylindrical roller bearings play a pivotal role in modern engineering and industrial applications due to their robust performance and versatility. Understanding the different types of cylindrical roller bearings can significantly enhance system efficiency and longevity. This guide delves into the various types, emphasizing experience, expertise, authoritativeness, and trustworthiness to provide a comprehensive overview.
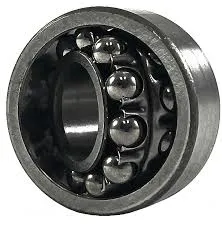
Cylindrical Roller Bearing Types An In-Depth Exploration
Cylindrical roller bearings are designed primarily to carry heavy radial loads and perform exceptionally well in high-speed applications. Their construction ensures minimal friction, allowing them to sustain large amounts of stress. The differences among the types primarily relate to the flange configurations and bearing capacity, each offering distinct advantages for specific use cases.
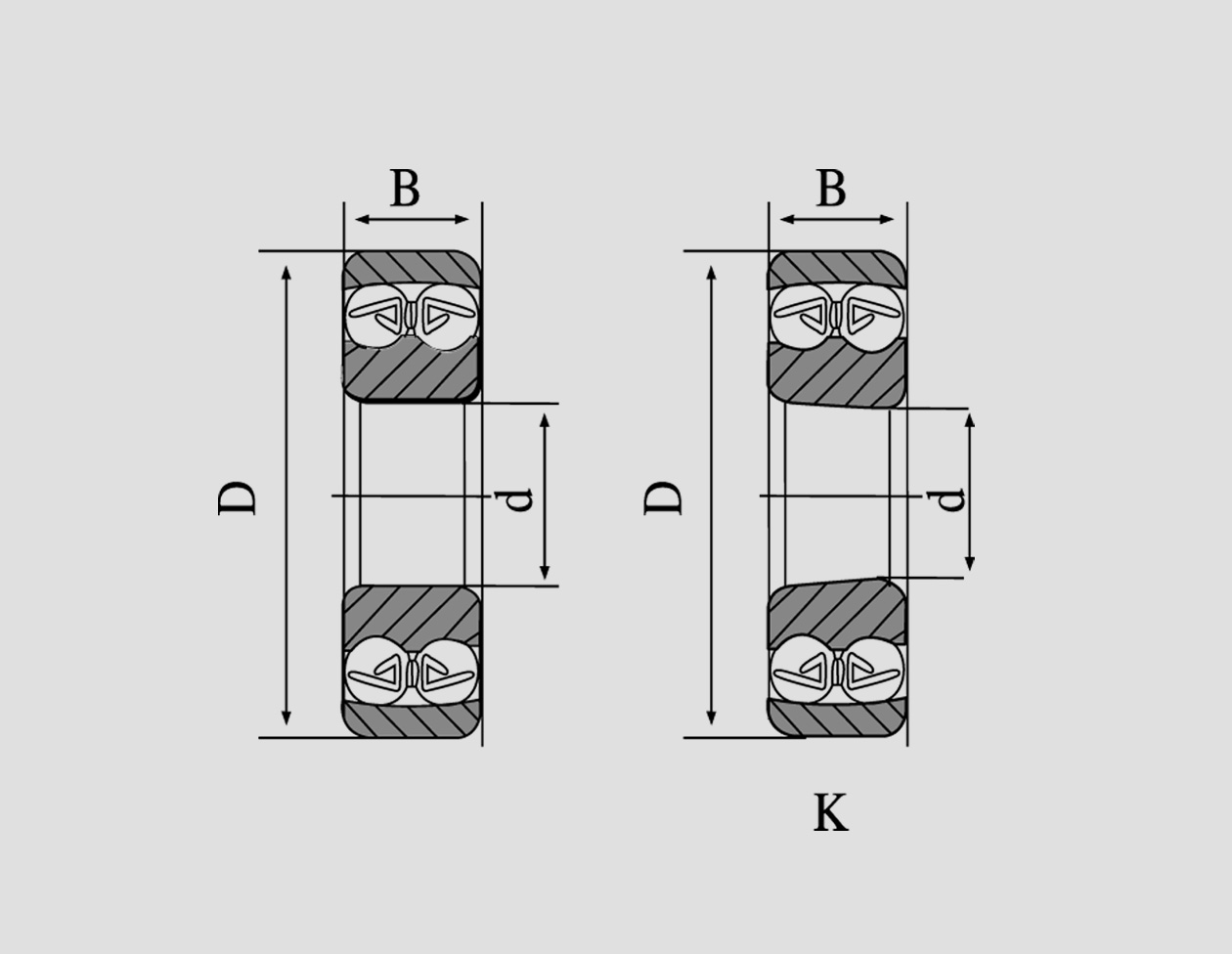
1. Single-Row Cylindrical Roller Bearings
Single-row cylindrical roller bearings are commonly used due to their simplicity and efficiency in handling high radial loads. These bearings contain a single set of rollers and are further divided based on their design
- NU Series These bearings have two flanges on the outer ring, enabling displacement.
They are ideal for free-end bearings.
- N Series With two flanges on the inner ring, this type allows shaft and housing movement, suitable for non-locating positions.
Personal experiences in industries such as automotive and electric motor manufacturing entail that choosing between the NU and N series often focuses on ensuring axial displacement capability without compromising performance.
2. Double-Row Cylindrical Roller Bearings
This type is engineered to deliver superior performance with higher radial load capacities. Double-row bearings are essential in applications that demand reduced friction and increased rigidity, such as in gearboxes and pumps.
The expert rationale for opting for double-row configurations often aligns with scenarios requiring more stability and reduced risk of roller misalignment. They are recognized for their operational trustworthiness, especially under challenging conditions.
3. Full-Complement Cylindrical Roller Bearings
These bearings omit the traditional cage, allowing a greater number of rollers. The absence of a cage maximizes load-carrying capacity but may reduce speed capabilities due to increased friction.
Experienced technicians highlight their use in low-speed applications with heavy loads, serving well in industries like mining and construction. The absence of lubricant-friendly cages typically necessitates a more rigorous maintenance schedule, emphasizing the need for monitoring and regular lubrication to ensure reliability.
cylindrical roller bearing types
4. High-Capacity Cylindrical Roller Bearings
Offering a combination of thin cross-sections and increased rolling elements, high-capacity bearings deliver excellent load handling even in compact machinery setups. These designs often implement advanced materials and technologies, reflecting significant expertise in minimizing weight while maximizing performance.
In sectors such as aerospace and high-performance racing, the employability of high-capacity bearings underscores the industry's drive for innovation and efficiency.
5. Multi-Row Cylindrical Roller Bearings
This configuration often involves two, three, or even four rows of cylindrical rollers, suitable for extremely heavy-duty applications. The increased number of rollers proportionally matches the demands of heavy machinery used in steel mills and paper manufacturing.
Experts advocate for multi-row bearings where operational reliability is paramount because their design naturally accommodates axial expansion and radial loads without compromising structural integrity.
Authority in Selection and Maintenance
Selecting the appropriate type of cylindrical roller bearing necessitates a deep understanding of the machinery's operational environment and performance requirements. Engineers and technicians highly recommend adhering to industry standards (such as ISO and ANSI) to ensure compatibility and safety.
Furthermore, authoritative sources underscore the significance of regular monitoring and maintenance. Ensuring correct installation, alignment, and lubrication effectively extends bearing life and enhances operational trustworthiness. Implementing condition monitoring technologies helps preemptively identify potential issues, establishing a proactive maintenance strategy.
Conclusion
Cylindrical roller bearings remain integral to the backbone of industrial machinery, with each type offering unique benefits tailored to specific applications. By leveraging expertise and maintaining comprehensive knowledge of each type's characteristics and use cases, engineers can significantly improve machinery efficiency and lifespan. Employing trusted sources and adhering to industry standards further solidifies the role of cylindrical roller bearings in modern engineering endeavors, reinforcing trust and reliability in every application.