When selecting the appropriate bearing for a specific application, understanding the difference between spherical and cylindrical roller bearings is crucial. Each type has unique characteristics and applications, which can significantly influence machinery performance, longevity, and reliability.
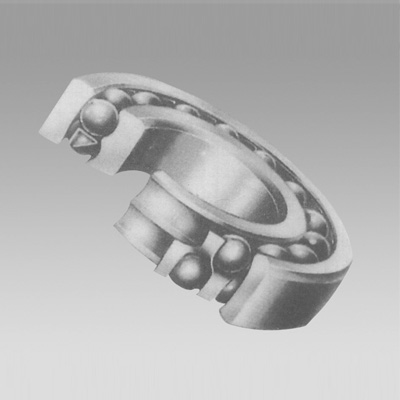
Spherical Roller Bearings
Spherical roller bearings are designed to handle high radial loads and moderate axial loads in both directions. They are characterized by their self-aligning capabilities, which stem from the spherical shape of their outer raceway. This design allows for angular misalignment between the shaft and the housing without compromising performance. Their ability to accommodate misalignment is particularly beneficial in industries where shaft bending or mounting errors are common.
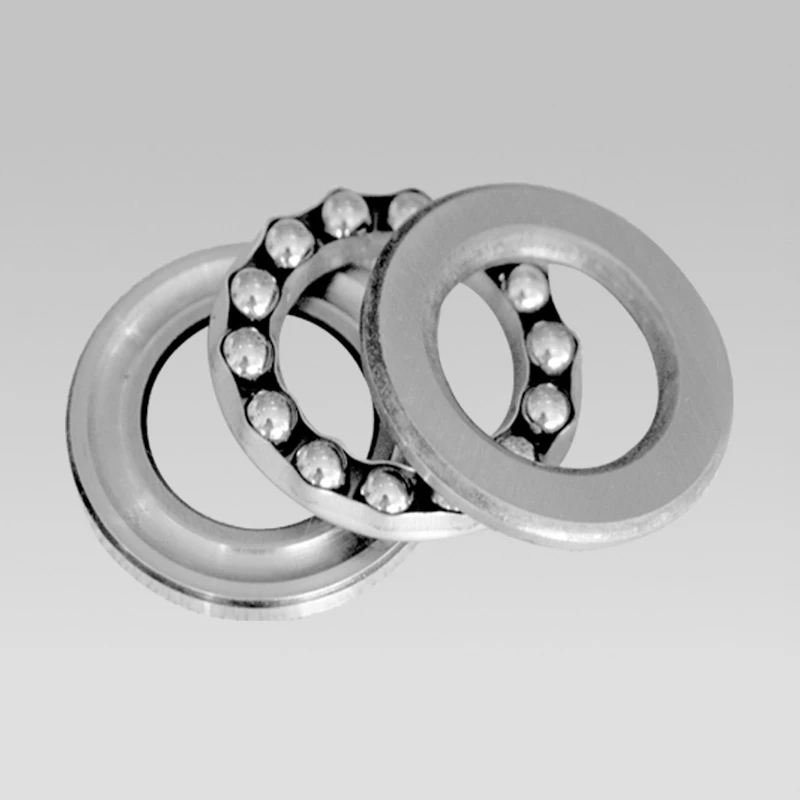
Industries such as mining, construction, and paper manufacturing often rely on spherical roller bearings due to their robustness and resilience in harsh operating conditions. These bearings also have a high load-carrying capacity, making them ideal for heavy-duty applications. The presence of two rows of rollers allows for enhanced load distribution and reduced risk of premature failure.
Cylindrical Roller Bearings
Cylindrical roller bearings, on the other hand, are optimally used in applications requiring high-speed performance and low friction. These bearings consist of rollers that are cylindrical in shape, allowing for contact with the inner and outer raceways over a larger area. This geometry is advantageous for high radial load capacities while maintaining excellent high-speed capabilities.
One of the distinguishing features of cylindrical roller bearings is their limited ability to handle axial loads, as opposed to spherical roller bearings. However, the different configurations, such as NU, NJ, NUP, and N, offer varying degrees of axial load support and mounting capabilities, providing flexibility for specific engineering needs.
Industries that demand precise rotational performance, like automotive, electric motors, and aerospace, often favor cylindrical roller bearings due to their accuracy and efficiency. They can be used in gearboxes, turbines, and pumps, where reliability and speed are paramount.
difference between spherical and cylindrical roller bearing
Choosing Between Spherical and Cylindrical Roller Bearings
The decision between spherical and cylindrical roller bearings should be informed by the specific demands of the application. Key considerations include load requirements, speed limitations, alignment issues, and environmental conditions.
In environments prone to misalignment and heavy loads, spherical roller bearings are often the superior choice. Their resilience against external shocks and ability to maintain performance amidst alignment errors make them a trusted option in challenging settings.
Conversely,
applications that prioritize speed and precision should consider cylindrical roller bearings. Their high-speed capabilities and efficient operation under significant radial loads match the rigorous demands of industries that cannot afford downtime due to misalignment.
Technical Expertise and Trustworthiness
For optimal bearing selection, consulting authoritative sources and industry experts is imperative. Manufacturers often provide detailed specifications and application guides that can assist in making an informed decision. Reliable suppliers should offer insights into material choices, lubrication options, and maintenance practices to enhance bearing longevity.
Establishing trust in bearing selection also involves considering the manufacturer's reputation and adherence to international quality standards. Bearings are critical components in machinery, and compromising on quality can lead to escalated maintenance costs and operational downtimes.
In conclusion, understanding the distinctions between spherical and cylindrical roller bearings is essential for engineers and procurement specialists focused on maximizing equipment efficiency and durability. By analyzing the specific application requirements and consulting with technical experts, businesses can ensure that their choice of bearings will lead to long-term success and operational reliability.