When choosing the right bearing for an application, deciding between cylindrical roller bearings and ball bearings can be crucial. Both serve important roles in machinery but differ fundamentally in design, performance, application suitability, and lifespan.
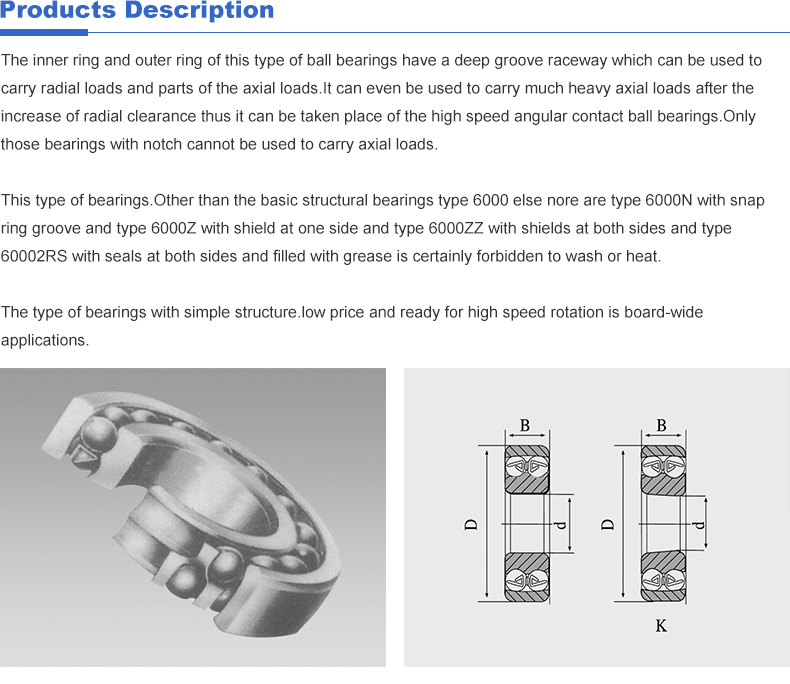
Cylindrical roller bearings excel in high-load capacity situations due to their design. The cylindrical shape of the rollers allows them to distribute weight more evenly over a larger surface compared to ball bearings. This characteristic makes them particularly advantageous in heavy industrial machinery, where they're employed to handle radial loads exceedingly well. Their ability to manage large radial loads makes them indispensable in applications such as gearboxes, electric motors, and turbines. Manufacturers often prefer cylindrical roller bearings in high-speed applications, as they can sustain their performance under demanding circumstances without compromising their integrity.
On the other hand, ball bearings are distinguished by their spherical balls, which provide less contact area but offer higher speeds with lower friction. This unique design makes ball bearings ideal for applications where speed trumps load. In environments that demand precision and efficiency, like consumer electronics or automotive applications, the low friction and precise movement offered by ball bearings make them the superior choice. They are excellent for sustaining both radial and axial loads, albeit lighter ones, compared to cylindrical roller bearings. Their versatility and ability to handle both types of loads efficiently underpins their use in applications from camera lenses to skateboards and hard drives.
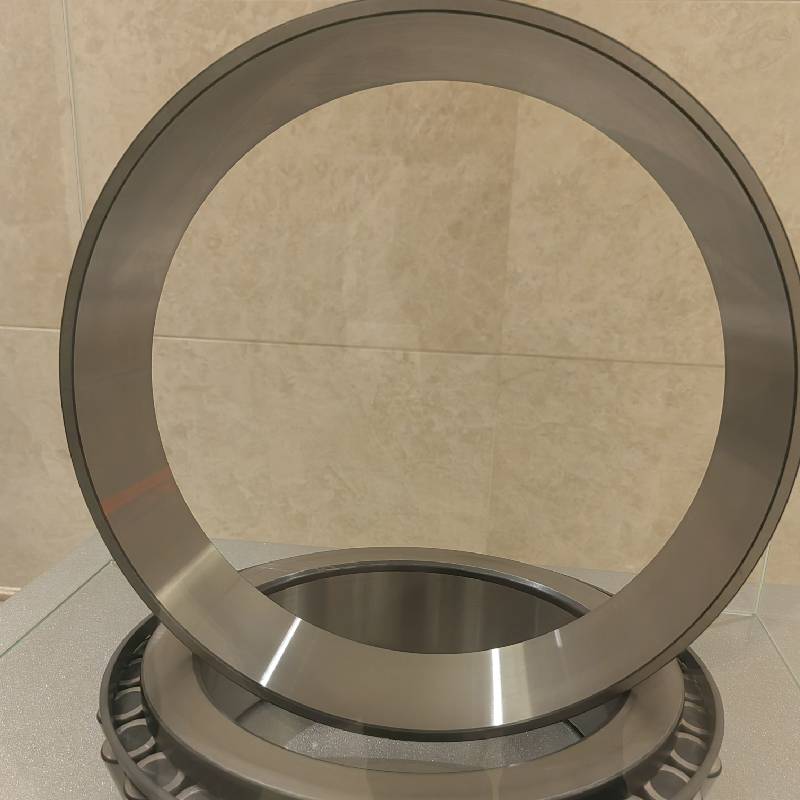
However, each bearing has its limitations. Cylindrical roller bearings, while excellent under radial load, are not as effective in managing axial loads. This limitation means they need to be paired with another bearing in applications where axial loads are present. Conversely, ball bearings, while efficient and versatile, have limitations regarding load capacity. They may experience quicker wear under heavier loads due to their smaller contact surface area. This means they need careful consideration in environments where both radial and axial forces are dominant.
cylindrical roller bearing vs ball bearing
In maintenance terms, cylindrical roller bearings generally demonstrate greater durability and longevity due to their design aimed at even load distribution. But, they might require meticulous lubrication regimes to maintain performance, particularly in environments with high-speed operations. Ball bearings, simpler in structure, often require less stringent maintenance but may necessitate more frequent inspections if they are operating close to their load limits.
When selecting between these two bearings, the application's specific requirements are paramount. If the application requires handling high radial loads or operates in high-speed environments, cylindrical roller bearings often provide the durability and performance needed. However, if the application prioritizes speed with lower radial and moderate axial loads, the precision and versatility of ball bearings are often unmatched.
Manufacturers and engineers must consider these factors load type and size, speed requirements, operational environment, maintenance capabilities, and longevity expectations. While cylindrical roller bearings may cost more initially, their lifespan under heavy radial loads could potentially offer cost efficiency in long-term operations. Ball bearings, often more affordable upfront, can provide adequate performance for moderate-load scenarios and applications prioritizing speed and precision.
In conclusion, the choice between cylindrical roller bearings and ball bearings must be grounded in a detailed analysis of application needs. Evaluating loading conditions, speed requirements, and maintenance scenarios will facilitate informed decisions, ensuring efficient and effective performance. By understanding each bearing's strengths and limitations, users can optimize machinery performance, minimize downtime, and extend operational lifespans, reinforcing the enduring importance of bearings in modern mechanical applications.