Deep groove ball bearings are widely used across various industries due to their simplicity and effectiveness in handling radial and axial loads. However, their prevalent usage doesn't overshadow certain disadvantages that can impact performance and application suitability. When selecting bearings for specific purposes, it's essential to consider these drawbacks to ensure optimal functionality and longevity.
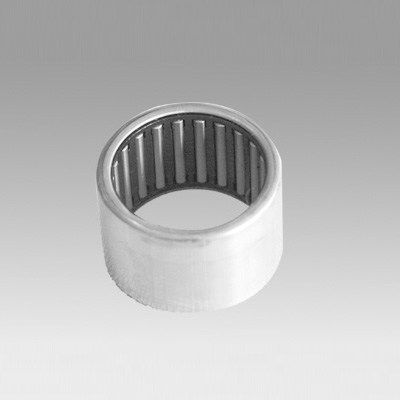
One significant disadvantage is the limited load capacity. While deep groove ball bearings can handle a moderate amount of axial and radial loads, they are not suitable for applications involving heavy loads. Their design restricts the number of rolling elements that can be accommodated, which limits their ability to support heavy forces. Industries that require bearings to carry large loads might find spherical or cylindrical roller bearings more effective, which can handle higher load capacities due to their design differences.
Another concern is their performance at high speeds. Deep groove ball bearings can operate efficiently within a moderate speed range, but they may not be ideal for applications that demand extremely high rotational speeds. At increased velocities, these bearings can experience a rise in friction and heat generation, potentially leading to premature wear or failure. In applications like high-speed turbines or motors, specialized bearings such as angular contact or ceramic hybrids are often preferred due to their ability to perform better under high rotational speeds without compromising efficiency and durability.

Furthermore, susceptibility to axial misalignment is another shortcoming of deep groove ball bearings. Although they can accommodate a limited degree of misalignment, larger variations can lead to increased internal stress and a reduction in bearing performance. This sensitivity to misalignment can cause uneven load distribution on the bearing raceways, leading to accelerated wear or eventual failure. Applications with potential misalignment issues might require self-aligning bearings, which can effectively handle such challenges through their design.
disadvantages of deep groove ball bearing
Moreover, the installation and maintenance of deep groove ball bearings require precise handling to ensure optimal performance. Improper mounting techniques can lead to uneven load distribution or increased internal clearance, which adversely affects bearing life. Maintenance practices, such as lubrication, need to be diligently followed to prevent contaminants from entering and damaging the bearing. Industries with harsh environments or complex operational setups might need to explore bearings with advanced sealing mechanisms or those designed for harsh conditions to mitigate these risks.
Additionally, deep groove ball bearings might not be the most cost-effective solution in specific scenarios. Although they generally offer a good balance of performance and price, the need for frequent replacement due to wear in demanding applications can accumulate costs over time. In critical operations where downtime is costly, investing in higher quality or specialized bearings could provide long-term savings and reliability.
Lastly,
noise and vibration issues can arise in some deep groove ball bearing applications. While generally quiet, certain applications can exacerbate their operational noise, especially under improper lubrication or when running at the extremes of their speed capacities. This can be a significant consideration in environments where noise levels need to be controlled, such as in medical equipment or high-precision machinery.
In conclusion, while deep groove ball bearings offer numerous benefits such as versatility, ease of installation, and cost-effectiveness, they are not without their disadvantages. Understanding these limitations, including load capacity restrictions, sensitivity to high speeds and misalignment, and maintenance challenges, is crucial for selecting the appropriate bearing type. For applications where these factors play a critical role, exploring alternative bearings with enhanced capabilities might provide a more suitable and sustainable solution. By acknowledging these aspects, businesses and engineering teams can make informed decisions that align with their performance needs, operational demands, and budget constraints, ultimately optimizing machinery effectiveness and lifespan.